Currently, our group is working on assembling our scaled parts with the other teams(steering & braking, suspension and guideway). As everything is coming together, we are making adjustments to our parts. Stress analysis is being done to double check that all our parts will not fail once scaled down and adjusted.
Additionally, we are working on our subteam portion of the final report. As of now, all parts of the report have been assigned to different group members. Based on our timeline, we are set to finish and submit our portion to the librarians by the December 12th deadline.
Monday, December 7, 2015
Thursday, November 26, 2015
Wednesday, November 18, 2015
Final Fail Safe Designs
Over the weekend we were able to finish making our designs. After a lot of trial and error, we finally decided to put the upstop wheel on the bogie. Keeping it stable would allow it to be more reliable. It would also move away from only being useful as long as the steering mechanism didn't fail. We've decided to place it in an empty portion of the bogie that already has a hollow square bar in place. Additionally, we designed the hooks and placed them on our system.
With our designs in place, we are now focusing on stress analysis. Also, we are waiting for the other sub-teams designs so we can start putting everything together and making any adjustments to the design to make sure it all fits. Our current worry is that the upstop wheel may be in the way of the steering mechanism. The suspension system also may get in the way of the hooks or the third bogie. We have kept all of this in mind, so we know our designs are adjustable, we'll just need to see where everything goes when assembled.
Today we will be meeting with Professor Furman and Ron so they can give us feedback on our new designs.
Thursday, November 12, 2015
New Fail Safe Solidworks Designs
As we started to design the hooks in solidworks, we went through a couple designs to ensure that the hooks would actually catch the way we would want as well as catch even when the track is switching. Additionally, we met with Bengt on Veteran's day to show our designs to him. After showing him our design, he agreed with what we had in mind, stating that there wasn't too much else we could do to mechanically catch everything.
At this time, we were finally able to start addressing the upstop wheel, which is a fail safe that we wanted to implement to help stabilize the bogie as it traveled on inclines and declines. Our main cause for putting off this design was that we planned to add it onto the steering mechanism. Because we've been unsure of how the steering team would be making their design, we waited for them to finalize everything more. Since they met with Bengt the same day as our team, we were able to see their most final design and start brainstorming where to place the upstop wheel.
At this time, we were finally able to start addressing the upstop wheel, which is a fail safe that we wanted to implement to help stabilize the bogie as it traveled on inclines and declines. Our main cause for putting off this design was that we planned to add it onto the steering mechanism. Because we've been unsure of how the steering team would be making their design, we waited for them to finalize everything more. Since they met with Bengt the same day as our team, we were able to see their most final design and start brainstorming where to place the upstop wheel.
Thursday, November 5, 2015
New Fail Safe Mechanism
As per Professor Furman's input, we met again to determine a new fail safe mechanism that would catch the bogie and cabin and keep it from falling off the railway in the case that the steering system failed. The biggest problem we had when addressing this situation was determining how to create a system that wouldn't change the guideway or the bogie much. Most of our ideas stemmed from adjusting the guideway, which was greatly discouraged.
After a lot of drawing and discussion, we were able to create hooks that wouldn't require any changes to the guideway and would be able to catch the bogie if it fell in a diagonal and/or downward motion. The hooks would be attached to near the top of the bogies, to hold on to the guideway if it went diagonally. There would also be hooks on the bottom that would catch the bogie if it fell downward. The hooks on the bottom would barely be above the guideway because we needed to keep the displacement low so the impact load would be low, which will put less force on the hooks so they don't break off.
After a lot of drawing and discussion, we were able to create hooks that wouldn't require any changes to the guideway and would be able to catch the bogie if it fell in a diagonal and/or downward motion. The hooks would be attached to near the top of the bogies, to hold on to the guideway if it went diagonally. There would also be hooks on the bottom that would catch the bogie if it fell downward. The hooks on the bottom would barely be above the guideway because we needed to keep the displacement low so the impact load would be low, which will put less force on the hooks so they don't break off.
Sunday, November 1, 2015
Project Update after Presentation 2
Based on Professor Furman's comments on our design in presentation 2, our group changed the failure situations we would be addressing for this year. In our presentation 2, we presented the addition of a third bogie and a ratchet and pawl system, which would be used during any inclines. The purpose of the third bogie was to help carry the load as well as add further redundancy in case the other two bogies failed. The ratchet and pawl system was a system we designed based on what we saw in rollercoasters; rollercoasters use this system to keep the cars from rolling back when they go up an incline.
Professor Furman asked that we create a fail safe system that would be able to catch the bogie. In our previous designs, we were expecting to use a fail safe in conjunction with the steering system. Professor Furman asked us to create on completely independent of the steering system in the case that it were to have a malfunction. With this in mind, we went back to brainstorming.
Fail-Safe Mechanism Presentation #2
The following URL will lead you to the second presentation for the Fail-Safe Mechanism https://docs.google.com/presentation/d/1lWFAE80qzSqN7ZtbFVaSHDX4EbZS058ueBsg3yqB-wE/edit?usp=sharing
Sunday, October 4, 2015
Fail Safe Mechanism Team Presentation #1
The Fail-Safe Mechanism team's first presentation can be found at this link: https://docs.google.com/presentation/d/1ATFZ6lAKB7cmCY3SRDIPFFEQnfBqu3Ifgul2lHmJqGQ/edit?usp=sharing
Sunday, September 20, 2015
Fail Safe Team Proposal
Bogie/Fail Safe Mechanism
The objectives of the bogie/fail safe mechanism are as follows:
- Bogie must be able to traverse up and down a guideway sloped at ±17° (30% grade) at TBD m/s
- Bogie cannot fall off the guideway despite failure of switching or main support wheels
- Bogie must have extra mechanism to help move cabin to prevent blocking the path
- Allow moving the cabin for fast unload of passengers
It will fulfill the design requirements listed below:
- Bogie must handle weight of cabin and all passengers inside
- Bogie must have multiple fail safe systems, (for wheels, cabin, switching mechanism,etc)
- Bogie must have a fail safe system that will prevent cabin from plummeting to the ground.
- Bogie must have at least a safety factor of 8
- Bogie must be able to still move when the fail safe system is initiated in order to travel to safe location where the bogie can be repaired, aka (Limp Mode).
- Bogie must meet city safety regulations
The objectives and design requirements will be proven through the construction of a
working model.
Sketches and Drawings
Bogie

Fail Safe
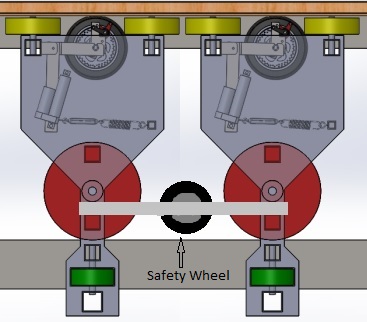
Sketches and Drawings
Bogie
Fail Safe
Fail Safe Team Introduction
For the Spartan Superway, the Fail Safe team will be focusing on creating fail safe mechanisms with the quarter scale model in mind. The Fail Safe team consists of the following people: Cassie Acosta, Steven Luong, Vicente Viqueria, Aaron Cheng, Christopher McCormick and Uday Ranjeet.
Scope of Work
Currently, the bogie design has been created to traverse a track with no elevation change with no fail safe mechanisms. The fail safe team will take on the tasks of redesigning the bogie to be able to make these elevation changes as well as create fail safe mechanisms to keep the bogie and cabin safe.
Goals
This year, the team's goals to complete by Spring 2016 are as follows:
Currently, the bogie design has been created to traverse a track with no elevation change with no fail safe mechanisms. The fail safe team will take on the tasks of redesigning the bogie to be able to make these elevation changes as well as create fail safe mechanisms to keep the bogie and cabin safe.
Goals
This year, the team's goals to complete by Spring 2016 are as follows:
- Re-design the bogie to traverse up and down a guideway sloped at ±17° (30% grade) at TBD m/s
- Design and build a fail safe mechanism by Spring 2016 that prevents the bogie from falling off the tracks.
Subscribe to:
Posts (Atom)